The Elite of Scotland
WHILE MURPHY IS AN IRISH NAME, THIS MURPHY IS SCOTTISH THROUGH AND THROUGH
By Nigel Smith
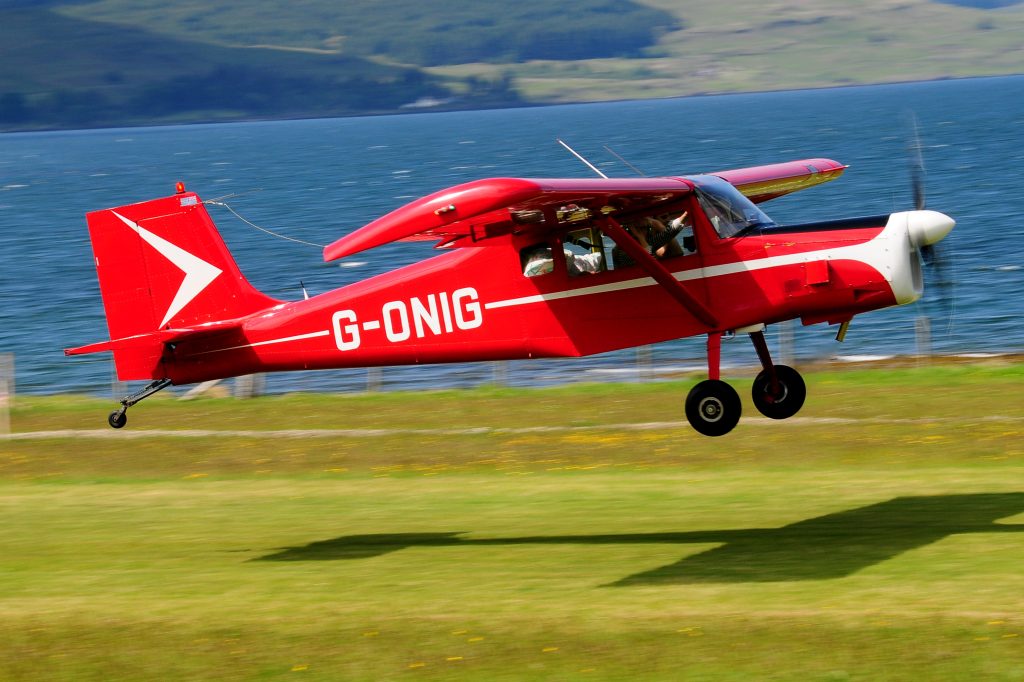
Meet G-ONIG, my Murphy Elite which started life as a kit project back in 2003. With the help of my son and engineering friends at work, I considered it complete with the installation of the Murphy 1800 amphibious floats in 2021, which had been planned from the start.
The build began in a wooden shed behind our house and, as each part outgrew the workbench, it was hung on the wall awaiting the next stage. As I knew ONIG would spend much of its time on or around water, all parts were sprayed with Metaflex and all rivets dipped before being pulled. JC5 (protective film) was used on all surface joints. The Elite is assembled with Avex pop rivets and was built on a simple flat bench without the need for jigs. When the fuselage was ready to leave, we removed the end of the shed and rolled it out under a tent we’d built to keep it dry. As soon as the wings were finished, it outgrew the garden so, in 2012, we moved to the local airport for final assembly and flight testing as a taildragger.
Since then, it’s flown around 320 hours. During that time, the floats were being assembled in the shed and were finally ready to fit to the plane in August 2020.
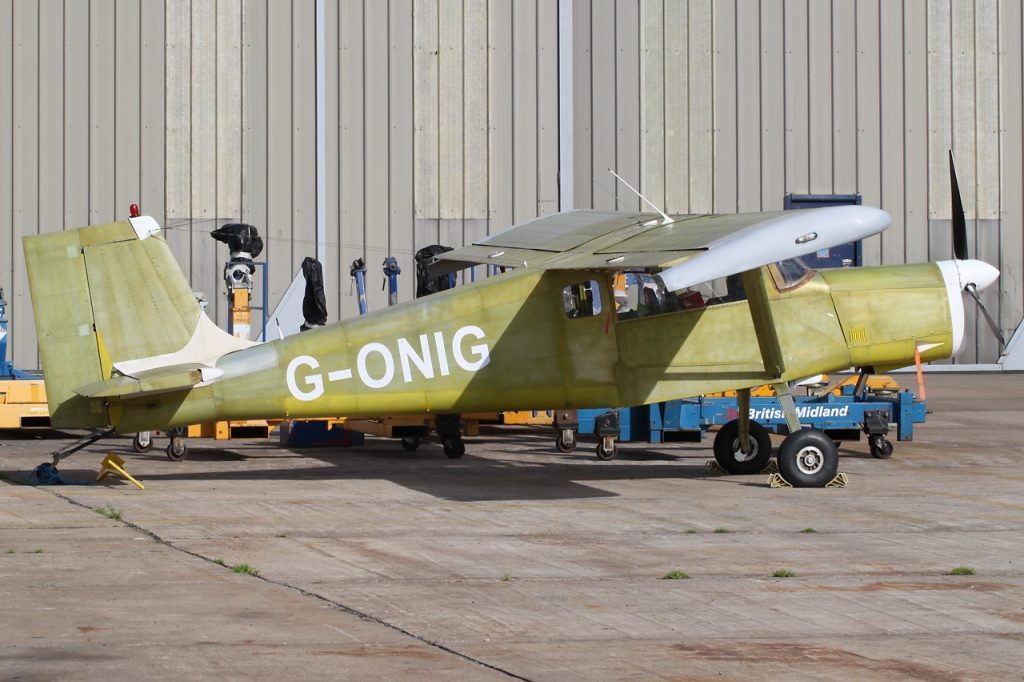
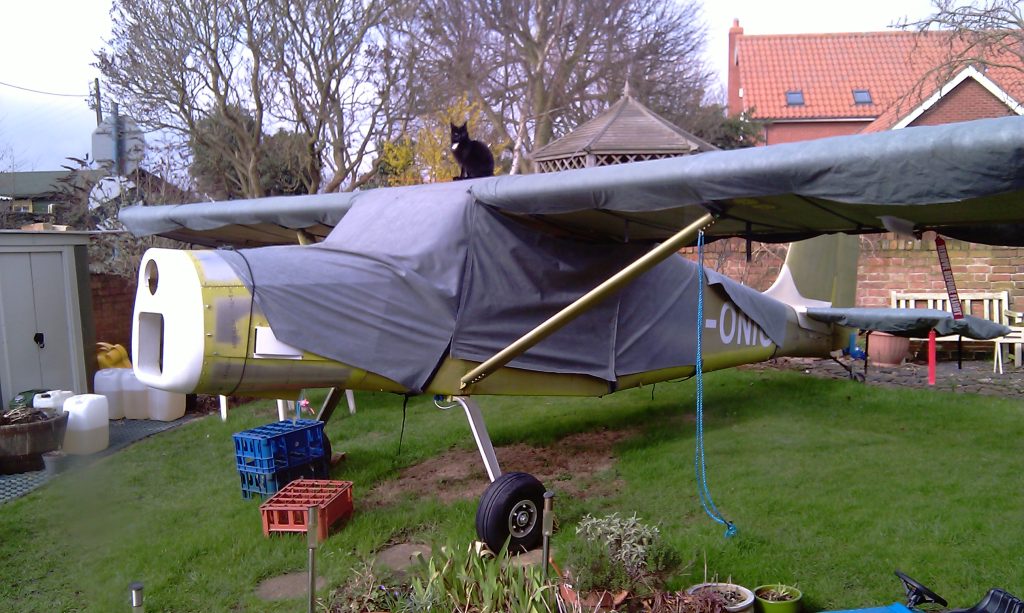
ONIG is powered by a Wilksch WAM120 turbo and supercharged two-stroke diesel engine burning around 16 litres per hour (4.2 gph) of Jet A-1. An MTV-6 seaplane prop gives a really smooth-running engine, and it happily purrs along at around 83 knots as a taildragger, and whilst that’s not particularly fast, the scenery in Scotland is far too beautiful to rush past.
The floats are all-aluminium (6061-T6 like the airframe) and are available from Murphy in Vancouver as either straight (no wheels) or amphibious and as a kit, partial or fully assembled. As my previous efforts with a shrinker/stretcher had left something to be desired, I chose the partial option as forming the lower skins I thought would be quite a skill. There are eight watertight compartments in each float, giving a displacement of 1800 lbs per side. Each compartment has an access hatch and a bilge pumpout point to remove any water prior to flight. The hull is sealed during assembly with Proseal, Sikaflex or PRC as available.
Gear retraction and extension is achieved by a hydraulic hand pump in the cabin. The nosewheels are fully castoring, so ground steering is by differential braking. Suspension in the main gear is through a sandwich of rubber doughnuts on each leg. Cables link the air rudder to the two water rudders, one on each float. I’ve fitted each with a sacrificial zinc anode to reduce float corrosion. Another cable to the cabin raises them when not needed. There’s a paddle fastened to the left float in case you find yourself up ‘S**t Creek’. The floats are rigged to the aircraft to give between 3 and 3.5 degrees between float decks and chord line. Operation on salt water brings extra corrosion risks to floats and airframe so a good washdown with fresh water and a product such as Salt-Away after each sea trip is highly recommended.
As we’d been warned by others, the aircraft’s performance with the amphibs fitted was less than we’d hoped for. 100-hp max. continuous power just didn’t give us a safe climb rate with all the hills around here and, on completion of handling tests for U.K. acceptance, we sadly removed them again and went back to conventional gear. I’m planning an engine change next year to (probably) a Rotax 916 which, after acceptance flights, can allow the refitting of my amphibs.
In Scotland at the moment there are several Cessnas operating on floats, including a 172 offering seaplane training. There’s also a couple of places elsewhere in the U.K. offering a chance to splash around in an aeroplane, and you’ll need to sit a CAA Seamanship exam within a year of doing your training to get a SES (single-engine sea) rating.
I used to work in Labrador, Canada in the early 80s with a Turbo Beaver and, since then, I’ve dreamt of owning my own floatplane. Building G-ONIG has been a real adventure, and the colour scheme is a copy of the Beavers and Otters from that time. Planning and thinking time during the build meant it took somewhat longer than anticipated, but it’s ended up just the way I wanted it, so I’m glad it wasn’t rushed.
I’d like to thank everyone who’s helped me along the way, but mainly my wife and son, “Barney” and colleagues from BMI Engineering who taught me how to do it “right” when I started the project, the staff at Derby airfield and Paul Jones who did the initial test flying, Wayne O’Shea in Ontario for everything ‘Murphy’, and everyone at Peterhead Longside airfield where it now lives, waiting to explore the Highlands of Scotland.
Nigel ‘Nig’ Smith is a member of the Light Aircraft Association (LAA 030828) and the EAA (EAA 666086). He can be contacted at mobile@airnig.co.uk.
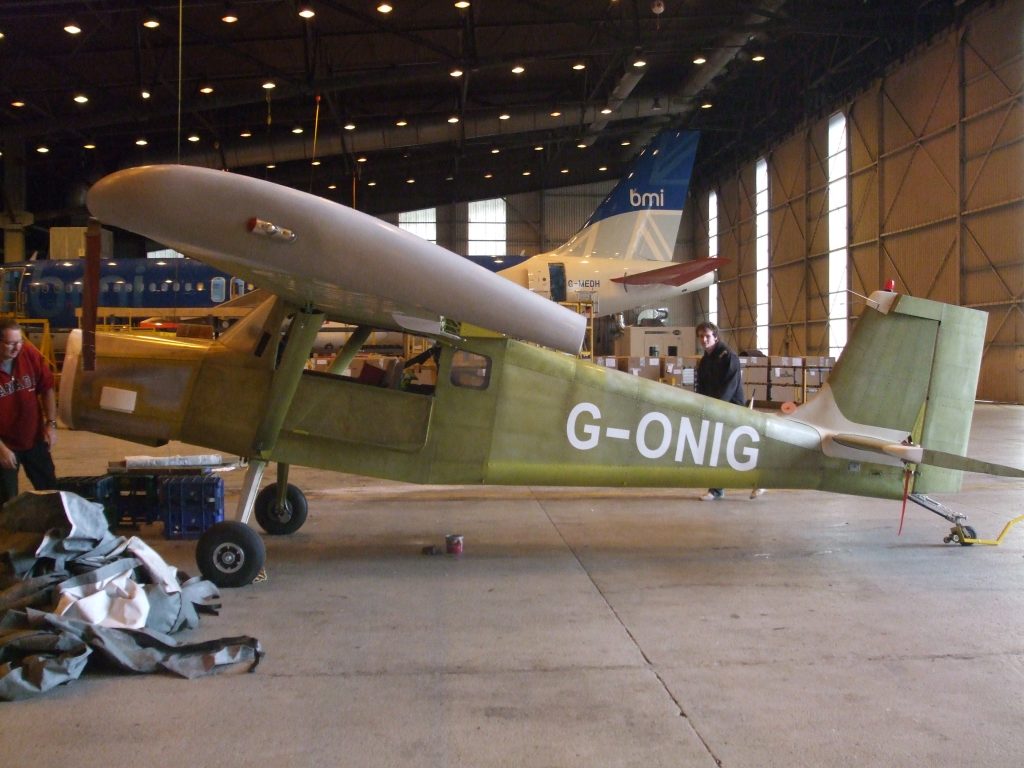
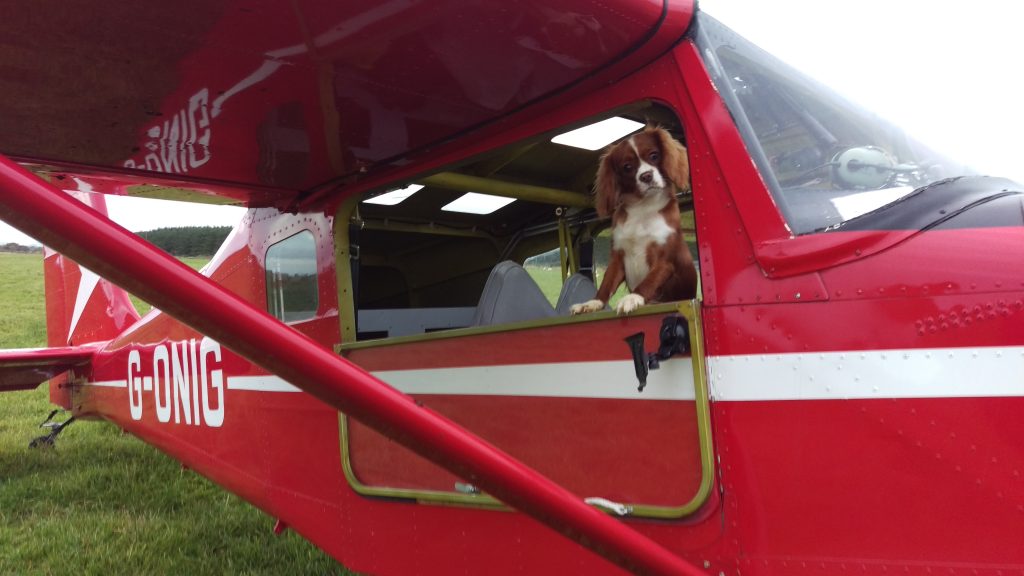
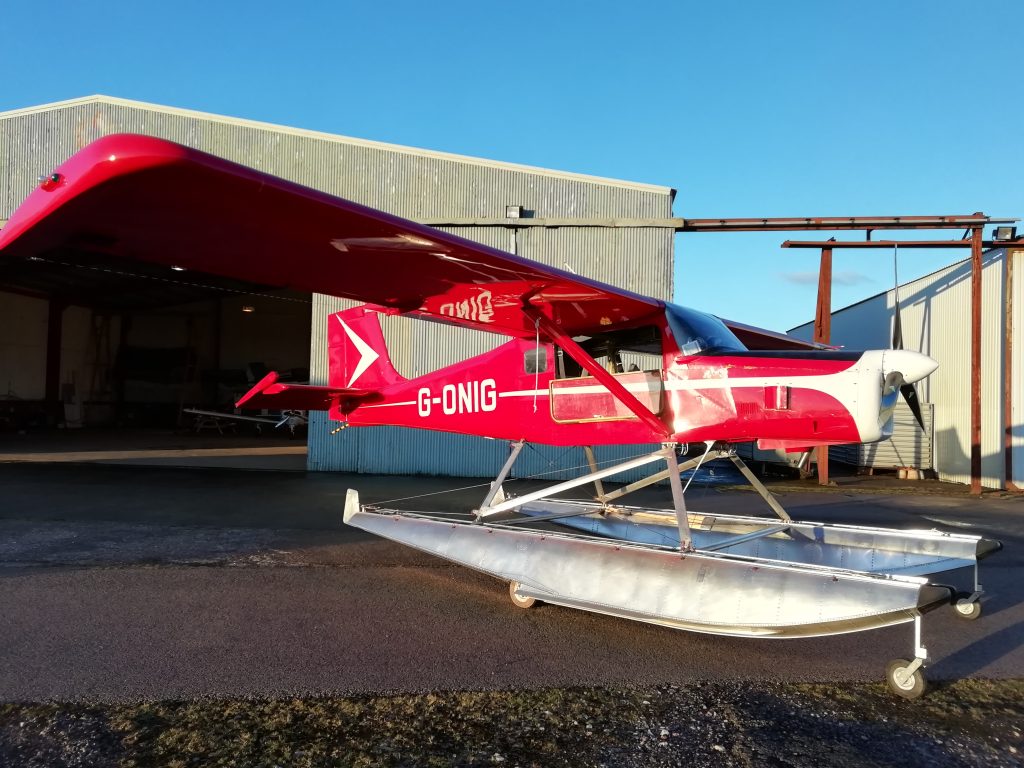
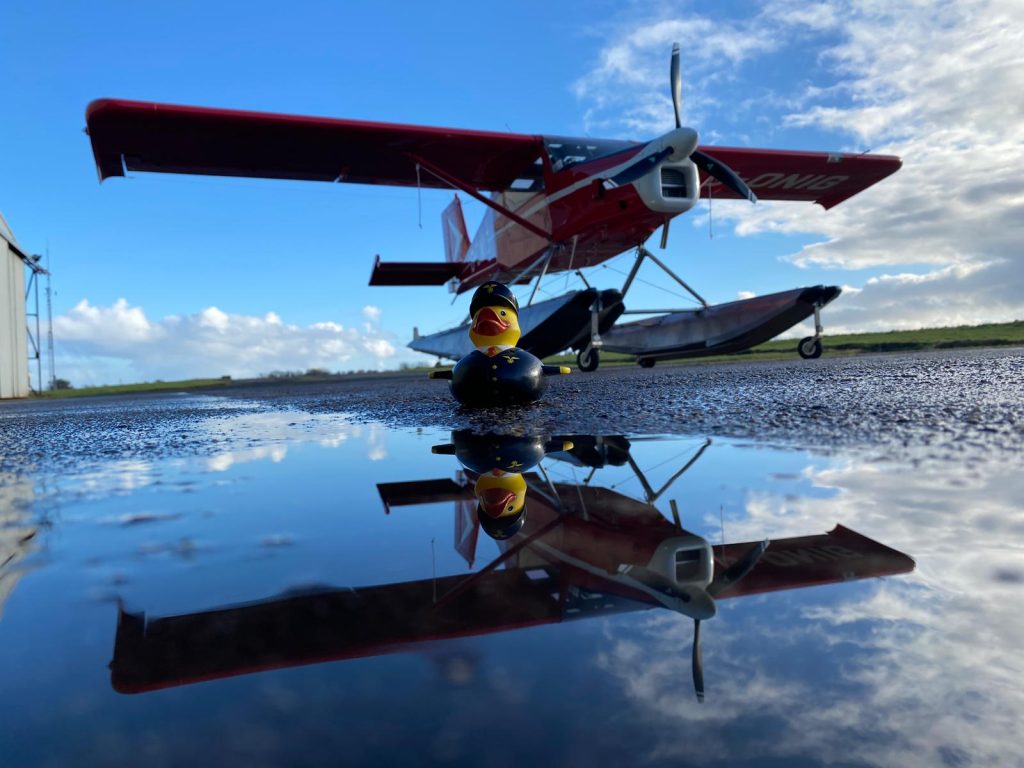